As the number of cars is increasing, the number of used tires is also increasing at the same proportion. This has led to the accumulation of the waste tyres in the environment causing pollution because of their non-biodegradable nature due to the complex materials making up the tyres and also the incineration of these tyres to reduce their numbers in the environment causes air pollution.
In order to sustainably manage environmental pollution associated with waste tyres, waste tyre to oil converting machines have been developed that operate based on the principle of pyrolysis. This involves heating the waste tyres in the reactor of a tire pyrolysis machine in the absence of oxygen to produce bio-oil and other useful end products such as carbon black, steel wire and biogas.
The process of pyrolysis using waste tyre is made possible due to the nature and composition of the raw materials making up tyres. These include natural rubber, synthetic polymers, carbon black, oil, steel wire and various chemicals.
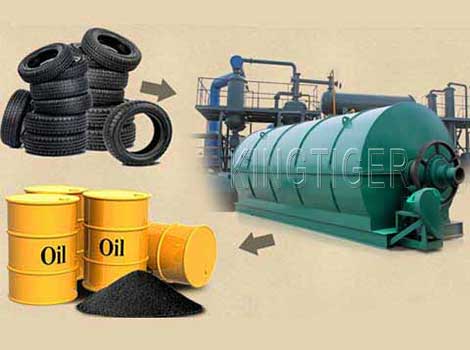
Tyre to Oil Machine
Components of waste tyre to oil machine
- A feeding system that feeds the raw materials into the reactor of the machine.
- An auto shredder that breaks down the waste tyres into the required size.
- A reactor that constitutes the main part of the tyre to oil machine where the heating process of the feedstock takes place.
- A casing that provides insulation onto the reactor.
- A manifold that separates light oil from heavy oil from the reactor.
- A hydro seal system that purifies combustible gases produced.
- A cooling system that is used to condense the oil gas from the reactor to form liquid oil.
- A discharging system for discharging the solid products from the machine.
- A de-dusting system that’s consists of a water spray, water washing and ceramic ring adsorption system which together clean the emissions from the machine before they are released into the environment. More: www.kingtigergroup.com/.
Working process of a tyre to oil machine
Using the feeding system, the waste tyre is fed into the machine where it is broken down using the auto shredder. The shredded tyres are then conveyed into the reactor which is heated at high temperatures in the absence of oxygen. As the temperature increases, oil gas is produced which is directed into the cooling system where it is cooled to produce liquid oil. This will then go into the manifold where heavy oil is separated from the light oil. The oil gas that cannot condense will go into the hydro seal system where it is purified and directed back into the reactor and used as fuel. The heavy oil separated in the manifold is directed back into the reactor since it has dust impurities where it is refined. When the process of oil production is completed, the temperatures of the reactor are cooled down, the final solid product containing carbon black and steel wire is then discharged from the discharge system where it can be collected.
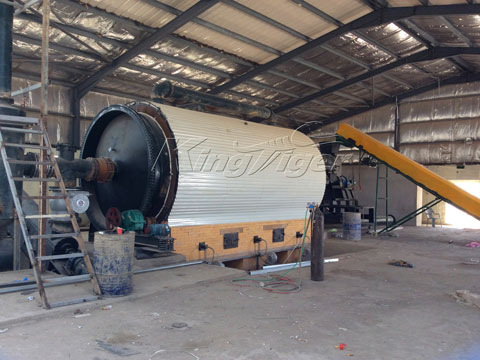
Tire pyrolysis machine
Uses of the final products of waste tire to oil production
1.Bio-oil
The total yield of bio-oil is estimated to be 45% 0f the total yield.
The bio-oil is used as an alternative source of energy in running industrial machines. When refined to diesel, the bio-oil can be used in running smaller machine engines.
2. Carbon black
The output of carbon black from the tire to oil machine is 35% of the total yield.
Carbon black can be used as a source of fuel. It can also be used in the construction industry in the making of construction bricks.
3. Steel wire
The amount of steel wire produced during the process is estimated to be 12% of the total yield.
The produced steel wire can be used in steel industries in making of new steel products.
4. Biogas
This is the least produced product which is estimated to be 8% of the total yield.
It is used as a source of fuel for burning in industries.
Advantages of using a waste tyre to oil plant
- The output of the final product is very high and the machine is designed in that you can add a catalyst that will speed up the process of carbonization thus increasing output.
- The machine does not require the use of a lot of fuel as the combustible gas produced can be recycled for heating in the reactor.
- The machine is safe to operate due to the presence of the insulating casing and a safety valve.
- It is environmentally friendly due to the presence of the de-dusting system that purifies smoke from the reactor. Also, the presence of the hydro seal system purifies combustible gas making it safe to use.